Infinity Machinery offers fully automated Bonnell spring production lines, encompassing detailed processes of quality inspection and performance testing. Through collaboration with engineers, they provide video records and inspection data to ensure the product's quality and performance meet the client's expectations. Additionally, Infinity Machinery provides customized design, installation and debugging, training services, and after-sales service, offering comprehensive support to clients.
In this shipment process, our sales representative visited the factory and collaborated with engineers to conduct comprehensive product inspection and performance testing, providing clients with detailed inspection data and video records. Here is our inspection and testing process along with the results:1. Inspection Process:
- The sales representative and engineer jointly inspected the appearance of the production line to ensure there were no damages or defects.
- Each component of the production line, including mechanical structures and electrical components, was inspected to ensure they were intact.
- Safety checks were conducted to confirm that all safety devices were complete and reliable.
2. Performance Testing:
- The operational stability of the production line was tested, including start-up, stoppage, acceleration, and deceleration under various working conditions.
- Production capacity of the production line was tested to verify if it meets the client's production requirements.
- Various working scenarios were simulated to check the adaptability and flexibility of the production line.
3. Video Records:
- We recorded the entire inspection and testing process and documented all data and operation details.
- The video clearly demonstrates the appearance, operational status, and functionalities of the production line, providing clients with intuitive references.
4. Client Inspection:
- All inspection data and videos were provided to the client for review and verification.
- Clients can evaluate the performance of the product through the video and determine if it meets their requirements.
Through this comprehensive inspection and testing, we ensure that the product's quality and performance meet the client's expectations, providing clients with reliable spring production solutions.
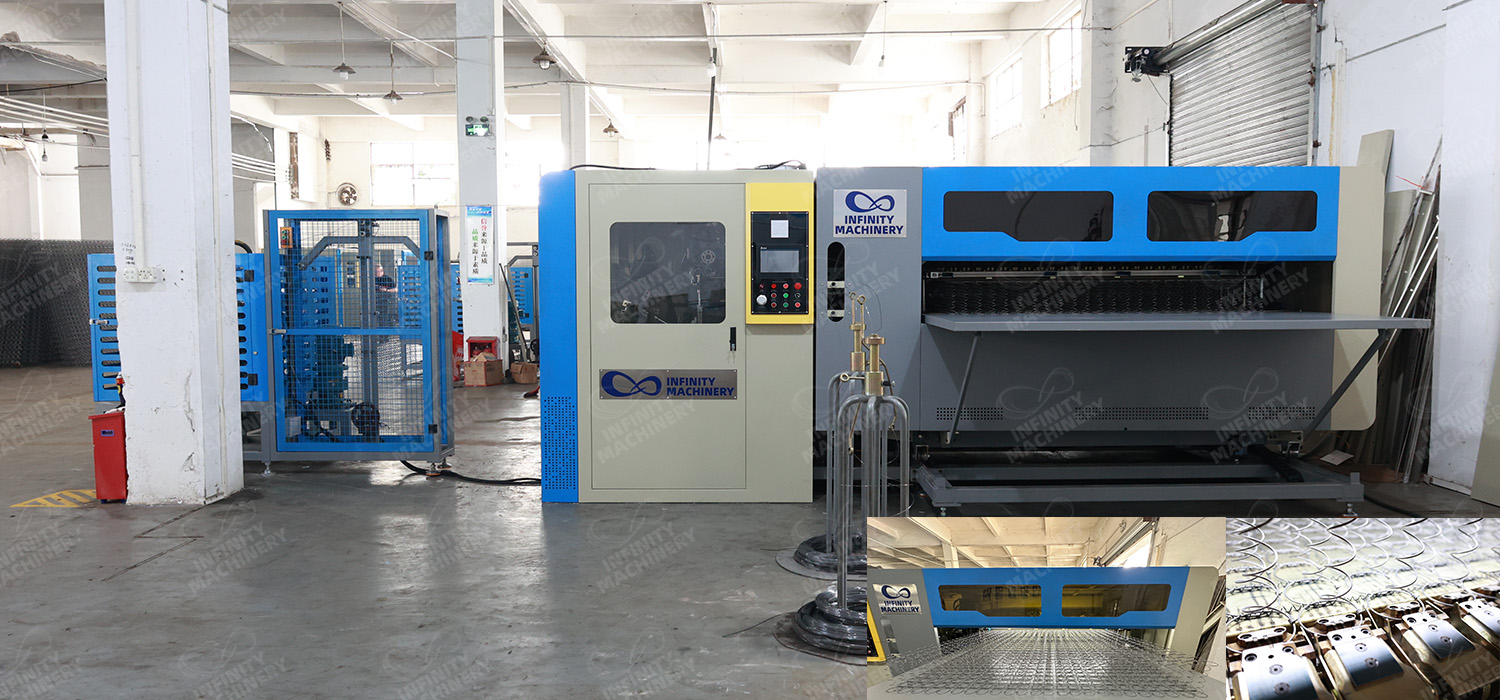
In addition to providing high-quality fully automated Bonnell spring production lines, our company also offers one-stop services to meet various needs in the spring production field. Our services include:
-
Customized Design: We provide customized design solutions based on the client's specific requirements, ensuring that the production line perfectly fits the client's production process and requirements.
-
Installation and Debugging: Our professional technical team is dispatched to the client's site to install and debug the production line, ensuring that the equipment operates smoothly.
-
Training Services: We offer operation and maintenance training to help the client's operators master the use and maintenance techniques of the production line.
-
After-Sales Service: We have established a complete after-sales service system, providing 24-hour quick response and technical support to ensure smooth operation for our clients.
Through our one-stop services, clients can enjoy comprehensive support from selection to after-sales, focus on spring production, improve production efficiency, reduce costs, and achieve greater commercial value.
More detail pls contact us.
Mail Landy: [email protected]
WhatsApp: +8618926236446